New business to make glass-blowing more accessible
Published 10:00 am Thursday, December 31, 2015
- Wells, at left, and Vinson display one of their finished glassblowing furnaces at the Americus Center for the Arts.
By MICHAEL MURRAY
michael.murray@americustimesrecorder.com
carpenter-media.go-vip.net.americustimesrecorder.com
AMERICUS — Anyone who has ever seen a motivational poster or logged onto the Internet has undoubtedly come across myriad quotes about how the secret to success in life is to do what you love and to do it well.
There are thousands of these quotes out there, attributed to wise individuals ranging from Confucius to Steve Jobs to Bob Dylan. In every instance, however, the theme remains the same: The secret to success is to be passionate about your life’s work.
Two individuals in Americus have recently embarked on a business venture that neatly embodies the spirit of these statements.
Charles Wells, a former Army Ranger who received his graduate degree from Texas Christian University, is currently a professor of three-dimensional art at Georgia Southwestern State University (GSW). Phil Vinson, the university’s fine arts shop technician, previously attended the Tyler School of Art in Philadelphia and has worked in a variety of glassblowing and blacksmithing studios since.
Together, the two have turned their passion for glass art into a successful business.
Mobile Glassblowing Studios, LLC was developed recently after Wells and Vinson decided to combine their love of blowing glass, their in-depth knowledge of the equipment used in glassblowing, and their collective desire to see the art form become readily available at an affordable price to artists all over the world. The organization currently employs seven people.
Located on 505 W. Lamar St., the business, still in its infancy, has bloomed from humble beginnings. Wells and Vinson originally began building their small, portable glass furnaces in Wells’ back yard in Americus. Their original inspiration for the undertaking was to create affordable furnaces for graduating glassblowing students from GSW, so that these students who have spent a great deal of time honing their craft will be able to continue on their artistic journey after college.
“We originally built a prototype for the college to do some outreach … ” Wells told the Times-Recorder.
The pair built the initial furnace as a promotional tool for the university because a mobile glassblowing rig can be used to reach a much broader audience than the permanent studio housed on GSW campus.
“We realized, almost immediately, that we needed two because Phil was wanting to go one way and I needed to go the other way,” Wells continued. “We were getting calls to come out and do things for different people at the same time so we built a second one.”
Before long, the glassblowing community, a relatively niche but very influential group in the contemporary art world, began to take notice.
“I was at the Arts Center doing some workshops and one of our alumni, Jesse Durham, came in,” Vinson said. “He decided that he wanted one of the furnaces out in Washington State, so he commissioned me to build one. [Charles and I] worked together on the design. I fabricated it for him and drove it out to him.”
Vinson stopped in Oklahoma City on his way to Washington to show the finished product to Wells, who was spending a portion of the summer working with a glass studio there with his brother.
“I pulled up and opened the trailer and, just the look on everyone’s face was priceless,” Vinson added.
From there, the pair knew that they were on to something big. They soon made plans to begin constructing affordable furnaces so that they can make the artistic medium that they are so passionate about available to a wide range of individuals.
Vinson had spent a great deal of time in California, particularly the San Francisco Bay area, where his wife Robin lived before moving to Americus. While there, he had built a network of connections in the glass artist community.
Last year, Vinson learned that the Glass Art Society, a group of glass artists from all over the world, would be holding their annual conference in San Jose, Calif.
Vinson and Wells saw this as the perfect opportunity to introduce their product to a large audience of glass enthusiasts, so they decided to build one to take to the conference.
“We weren’t even a company then,” Vinson said. “We just thought it’d be really cool.”
All the while, the pair continued receiving more and more calls from individuals who were interested in learning more about their furnaces.
They reserved a booth at the conference among other vendors who have been in the business, selling tools, colored glass bars, and other equipment for years.
“I had never been to one of these conferences, so it was a little overwhelming at first,” Wells said.
Vinson, who has attended several Glass Art Society conferences followed with, “For me, it was like … this is my entire reputation in the glass world. I’m putting it all on the line .. This is a big deal … I knew when I made the reservation that I was going completely all-in.”
Needless to say, the two budding manufacturers were nervous when they set up shop at the conference, as glass artists are known to be picky about the equipment they use.
“One of the guys waiting for us when we got there the first morning was a man who has been building [large scale] furnaces for 30 years,” Vinson said. “He had a big grin on his face. He was just super excited that we were [building these small furnaces].”
From there, both Wells and Vinson agree that the reaction to their product at the conference was overwhelmingly positive.
During the interview, Wells shared one of the more memorable experiences from the conference.
“I was talking to this one guy and I didn’t know who he was,” he said. “I told him all about how we want to keep the furnaces affordable for students graduating and make the medium accessible … and he totally got it. He later asked me, ‘Have you read my book?’ I wasn’t sure what he was talking about so I asked him, ‘What book?’ It turns out that this was the man who wrote the textbook that I use [when teaching glass at GSW]. That’s the level that we were on … I was talking to him about glass accessibility and how the whole thing has become an industry again … As it turns out, he literally wrote the book on the subject.”
Business has steadily increased for the pair since then and, most recently, they moved into their new facility on Lamar Street in November. They are currently working on completing their existing orders and expect to continue to stay busy as word of their product spreads through the artistic community.
On the demand for their product, Wells told the Times-Recorder, “There’s definitely a demand. It’s not huge. It’s a niche market … but I think we both have a soft spot for the accessibility of the material that’s driving some of this. We want more people to know about glass than currently do … I’m think that we can probably sell about four or five hundred in the United States. We’re on, I think, number 20 now.”
Vinson stated that they project the factory’s manufacturing capacity to reach up to 50 furnaces per year in the current facility.
“We’re trying to grow as quickly as we can, but keep it somewhat controlled,” he said.
They also have plans to open a retail space where they can sell glass pieces created using their equipment. A portion of the proceeds from the sales are intended to benefit the Americus Center for the Arts.
“Painters don’t mix their own paint or make their own brushes,” Wells said, on why he believes that what they are doing is so important. “Potters don’t make their own wheels. It’s not necessary, but it is really wonderful when people do know how to do these things.”
“Where there hasn’t been any access, we want to create as much access as we can to the equipment and materials,” Wells continued. “There are so many deserts out there where there’s no melted glass at all and we’re trying to fill up some of those places and let people just see it a little more.”
Mobile Glassblowing Studios, LLC has recently broken into the world market as well, selling a unit to an artist in India.
“This is the first, private, small-scale glass studio in India,” Vinson said. “This is the very beginning of the studio art glass movement in India.”
“We’re planning to send one of our people, Devon Cole, over there for two months to help get it up and running,” Wells added.
As anyone who has opened a new business can likely attest, embarking on that life journey can be nerve-racking.
“This is my first real exposure,” Wells said, near the conclusion of the interview regarding how it feels to put their product out on the world market. “It’s pretty terrifying, actually.”
Wells went on to say that, while he is acutely accustomed to taking artistic risks while working with this type of equipment, this is a completely new type of risk for him.
“I have a whole new respect for people that I see running a pool business or coffee business or whatever,” he said. “It’s a whole different perspective. It’s pretty remarkable to look out and see these people making a go of it … That’s a very wonderful risk.”
The pair also expressed enthusiasm that the venture will help stimulate the local economy, as the majority of the furnaces they’ve produced are being sold to individuals from all over the country and the world, thus bringing money into Americus that would have otherwise been spent elsewhere.
At the conclusion of the interview, Wells humorously pondered what would happen if the business were dissolved.
“If it doesn’t work, we may just have to open a barbecue restaurant here,” he joked.
“He does make a pretty good brisket,” Vinson added and they chuckled as they left the building.
Luckily for Vinson and Wells, as well as the City of Americus, it certainly does not look like it will come to that.
The duo’s knowledge and experience, combined with their love of the medium and their desire to inspire creativity in others, have built a solid foundation for a successful enterprise with a promising future.
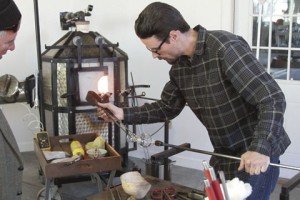
Warner Robbins-based glassblower, Chris Fiertner, gives a demonstration of the mobile unit’s capabilities during Mobile Glassblowing, LLC’s Open House on Dec. 19 in Americus.

Charles Wells Jr., at left, and Charles Wells Sr. carefully assemble the frame for one of Mobile Glassblowing, LLC’s unfinished portable furnaces.